Lost Wax Process
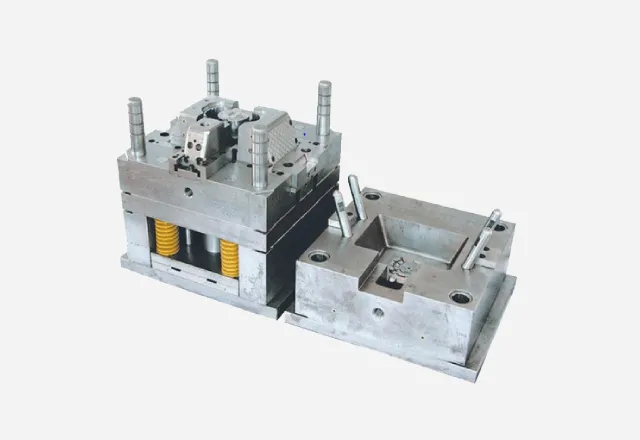
Step 1: Tool and Die Making
This initial step involves creating a master die or pattern, typically out of metal, which will be used to produce wax patterns.
Step 2: Wax Injection
In this process, molten wax is injected into the master die to form a wax pattern. This pattern is an exact replica of the final metal part.
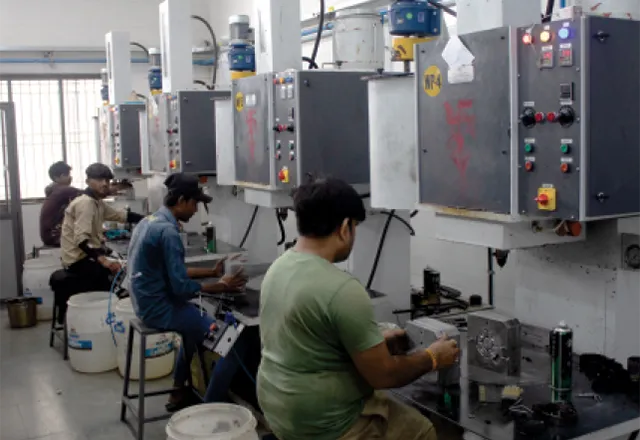
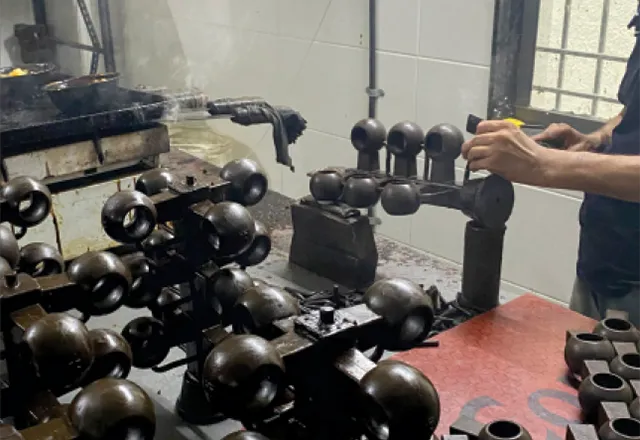
Step 3: Wax Assembly
Multiple wax patterns can be assembled together to form a tree-like structure which is created for casting multiple parts simultaneously. This is done by attaching the wax patterns to a central wax runner system, ensuring they are properly aligned for the coating process.
Step 4: Coating
The assembled wax pattern is repeatedly dipped into a ceramic slurry and sprinkled with fine sand to build up a hard shell. This process, known as shell building, involves multiple layers to create a robust mold capable of withstanding the casting process.
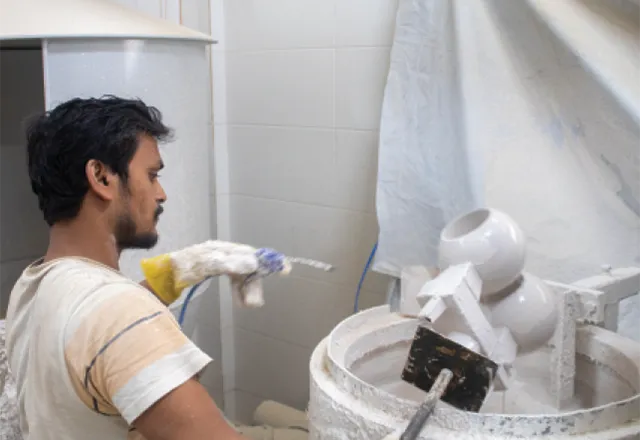
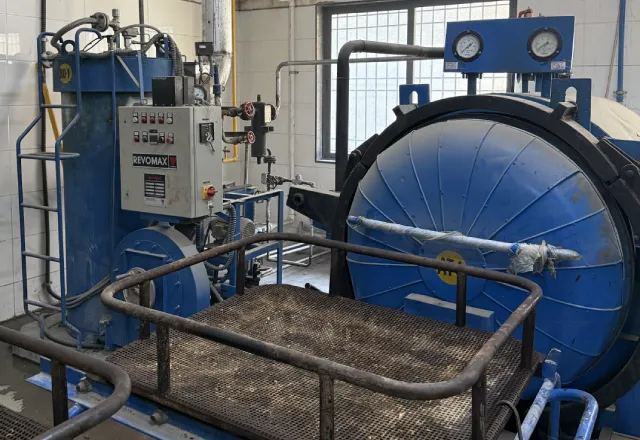
Step 5: De-Waxing
Once the ceramic shell has dried and hardened, the wax is removed through a process called de-waxing. This is done in an autoclave where heat and pressure melt and drain out the wax, leaving a hollow ceramic mold.
Step 6: Melting and Casting
The metal to be cast is melted in a furnace at very high temperatures. Common metals used include aluminum, bronze, steel, and other alloys. The choice of metal depends on the final application’s requirements for strength, durability, and other properties. The molten metal is carefully poured into the pre-heated ceramic mold, filling the cavity left by the wax. The mold is then allowed to cool and solidify, forming the metal part.
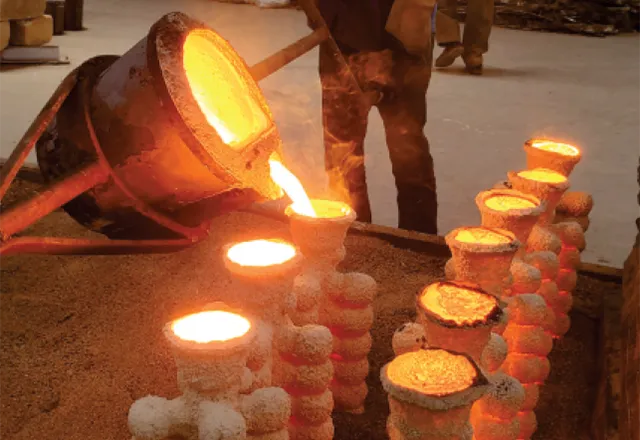
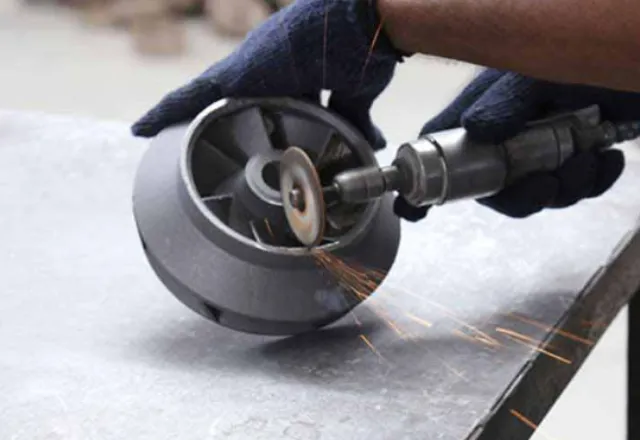
Step 7: Fettling
Once the casting has cooled and the ceramic shell is broken away, the cast parts undergo fettling. This process involves removing any excess material, such as runners and risers, and cleaning the surface of the cast part. Fettling can include knockout, cutting, grinding, shot blasting and to ensure a smooth finish and to prepare the part for final inspection.
Step 8: Inspection
After the metal has cooled and the ceramic shell is broken away, the cast parts are cleaned and subjected to rigorous inspection. This may include visual checks, dimensional measurement, and nondestructive testing methods to ensure the parts meet quality standards.
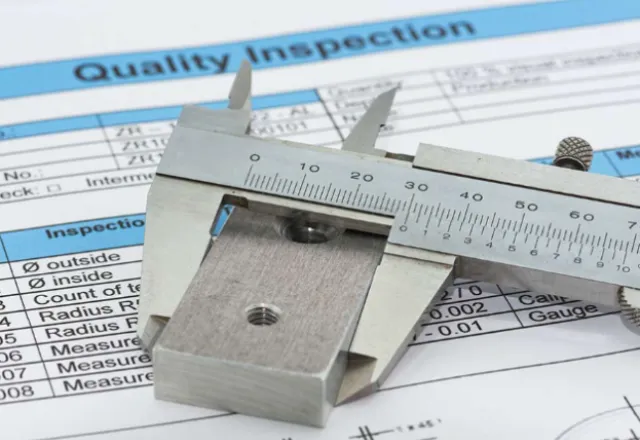